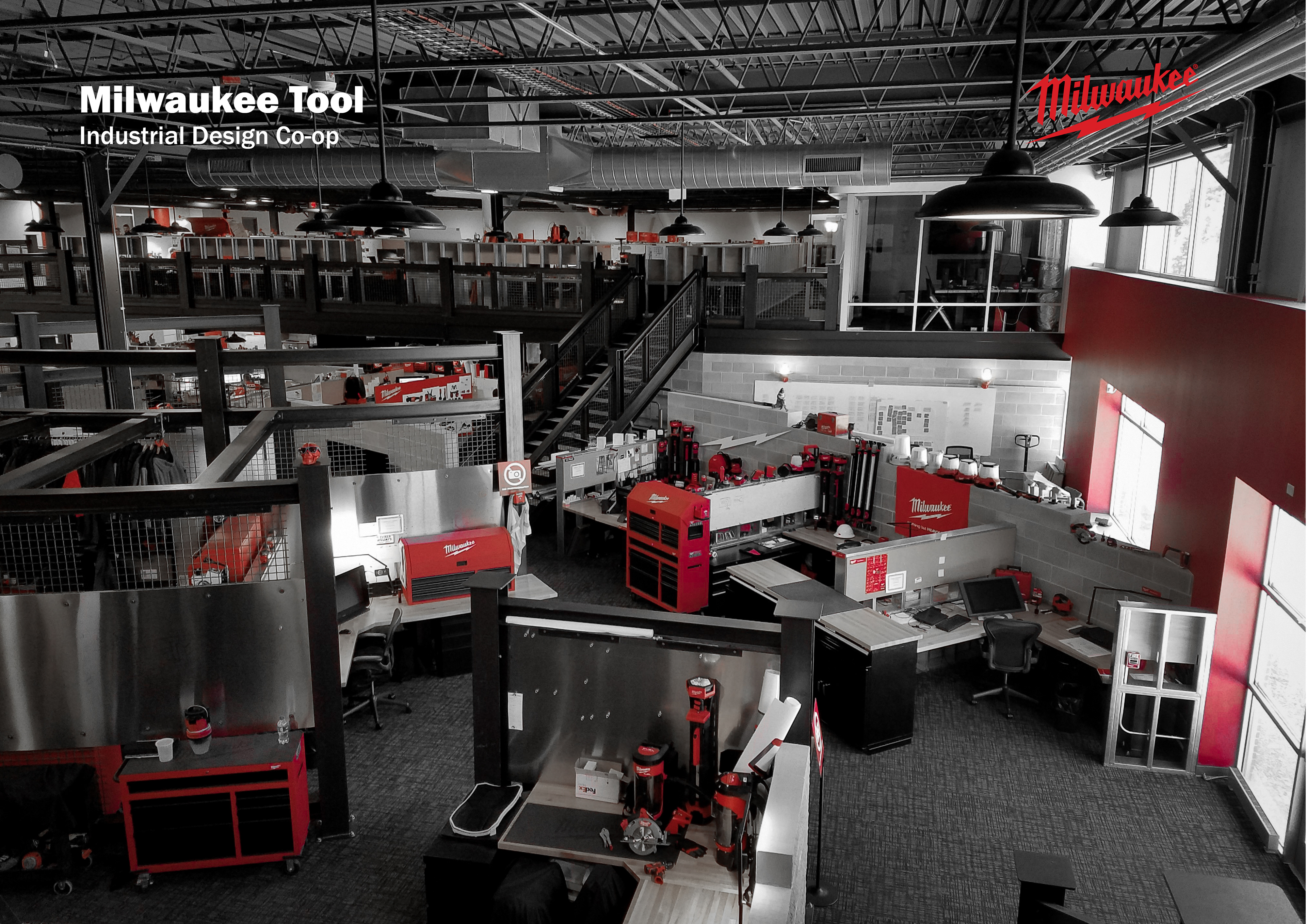
During the summer of 2018 I had the opportunity to work as an Industrial Design Co-op at Milwaukee Power Tools, in Brookfield Wisconsin. I worked on several projects in the Lighting and Lifestyle category, and got to contribute to all stages of the Milwaukee design process. This began with early ideation and form development, working around real internals, moving into rough CAD and prototyping. The work environment was fast-paced and focused heavily on early concept validation. I often presented my progress to the multidisciplinary teams, where I would receive feedback and hold group ideation sessions.
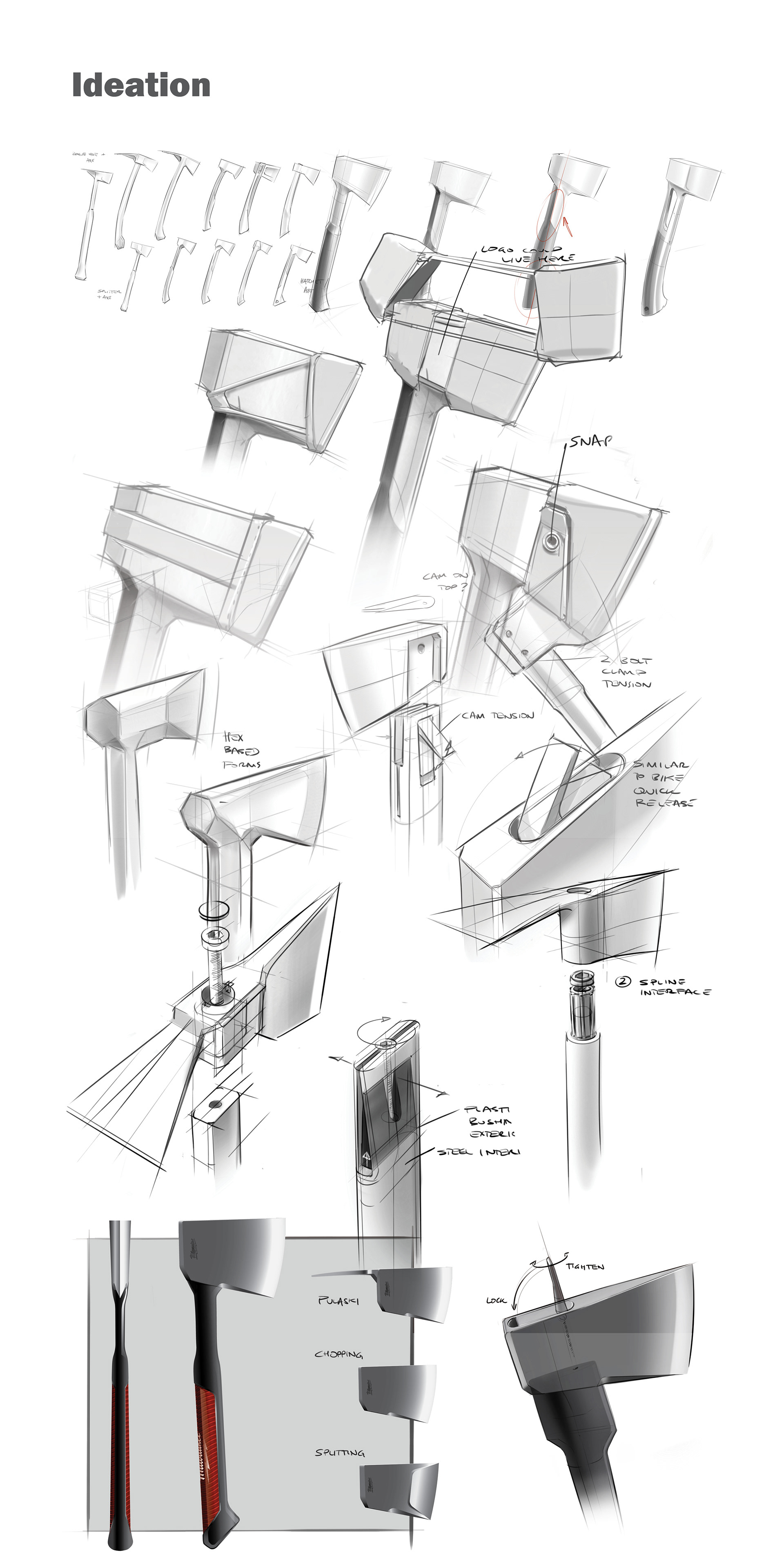
I began sketching hatchet forms in grayscale, sculpting angular forms in the heads that transition to ergonomic curves in the handles. I referenced basic hatchet proportions, working in my own interpretation of a future Milwaukee design language. Head swapping mechanisms and sheaths were explored, however I decided to focus on creating an “chopping” family of axes around a strong form.
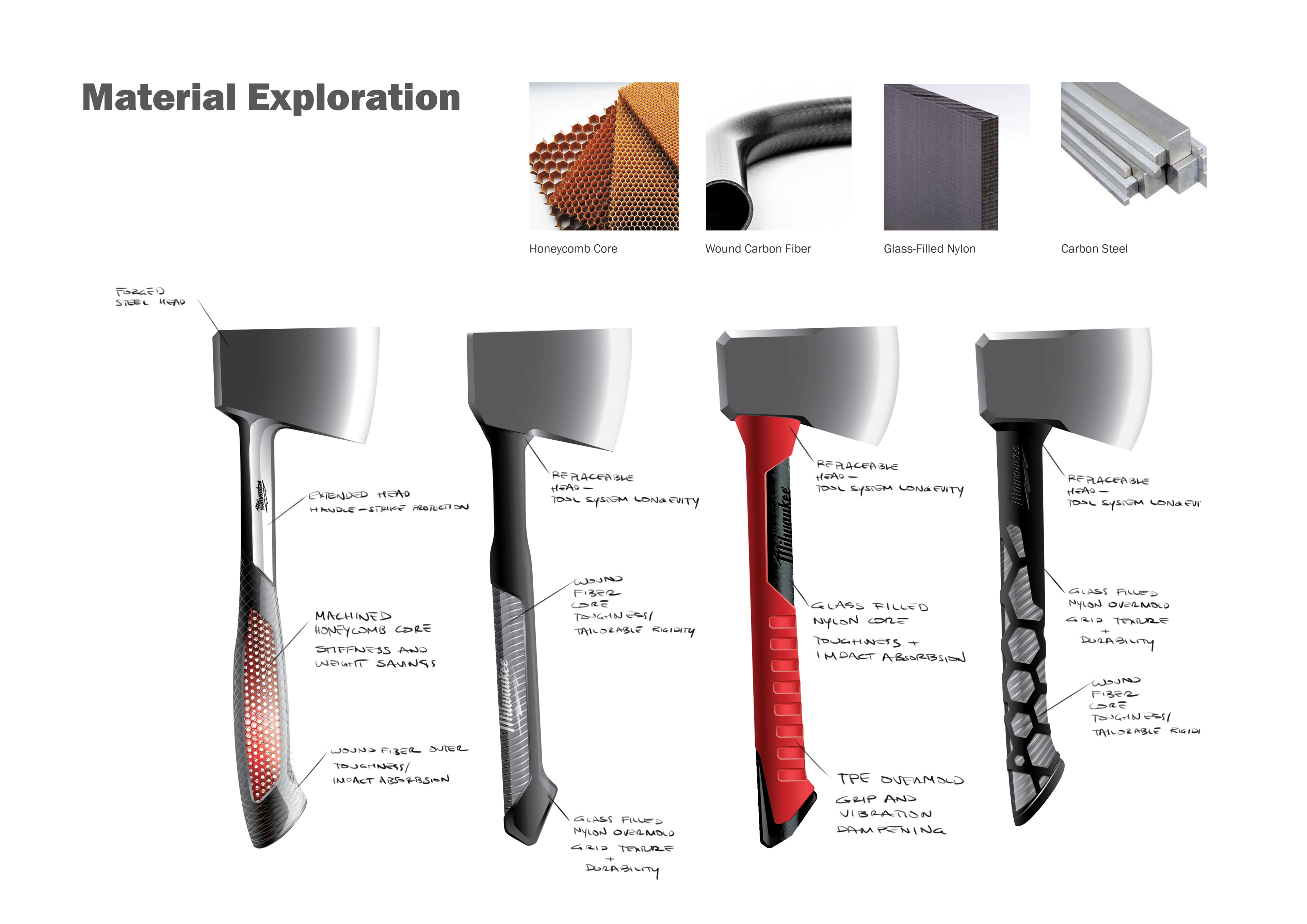
Referencing current Milwaukee design language, I researched and explored how material innovation could elevate the hatchet in both appearance and function. Composites utilizing honeycomb, wound carbon fiber, and glass-filled nylon can lighten the handle while improving strength and vibration dampening. These materials are visually interesting and have the potential to differentiate themselves from competitor products.
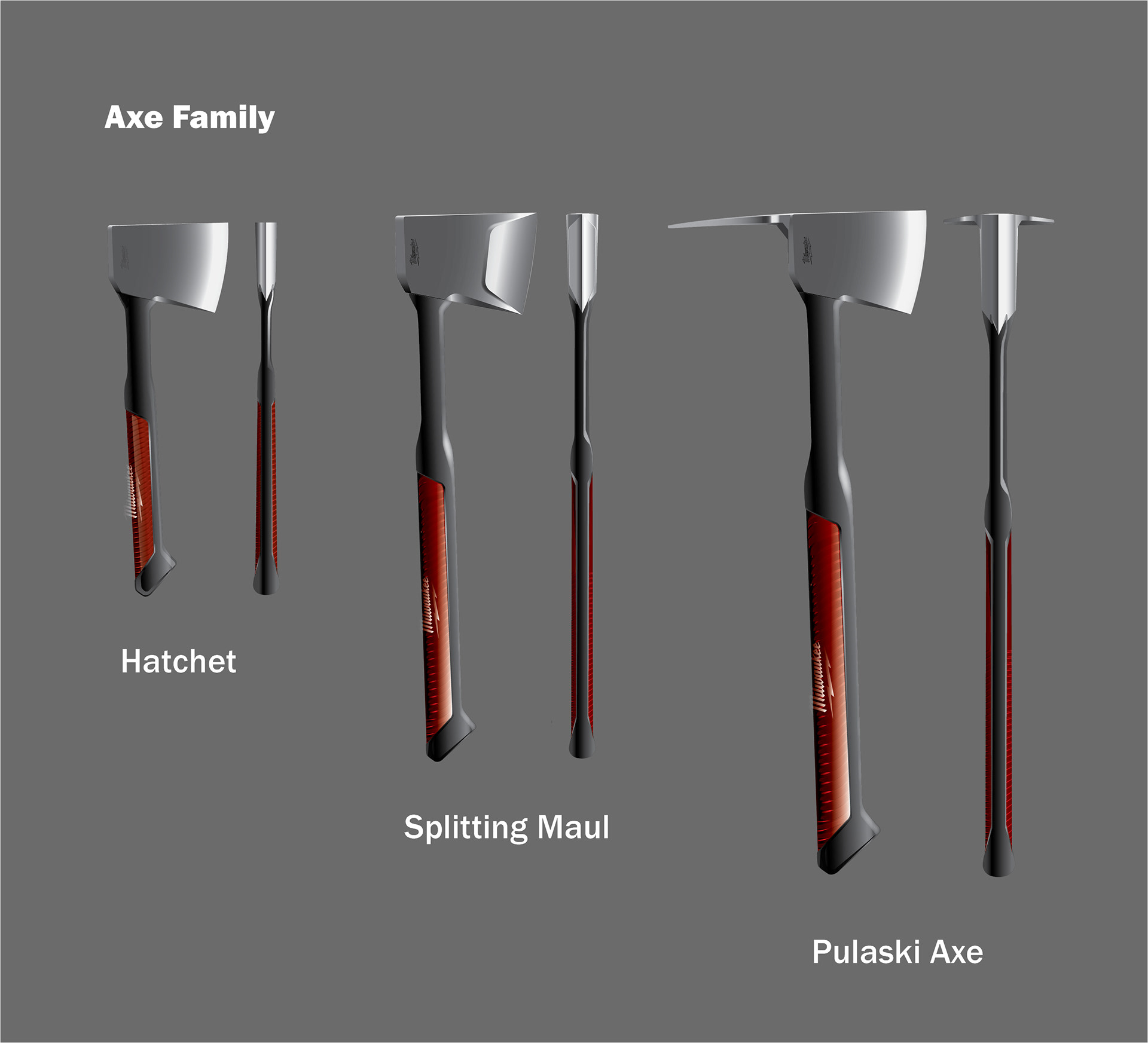
This exploration of future Milwaukee form and material resulted in two-dimensional concepts for an axe family. The family consists of three products, a hatchet, splitting maul, and Pulaski axe. These concepts strike a balance between targeting the professional contractor and appealing to the future Milwaukee consumer.
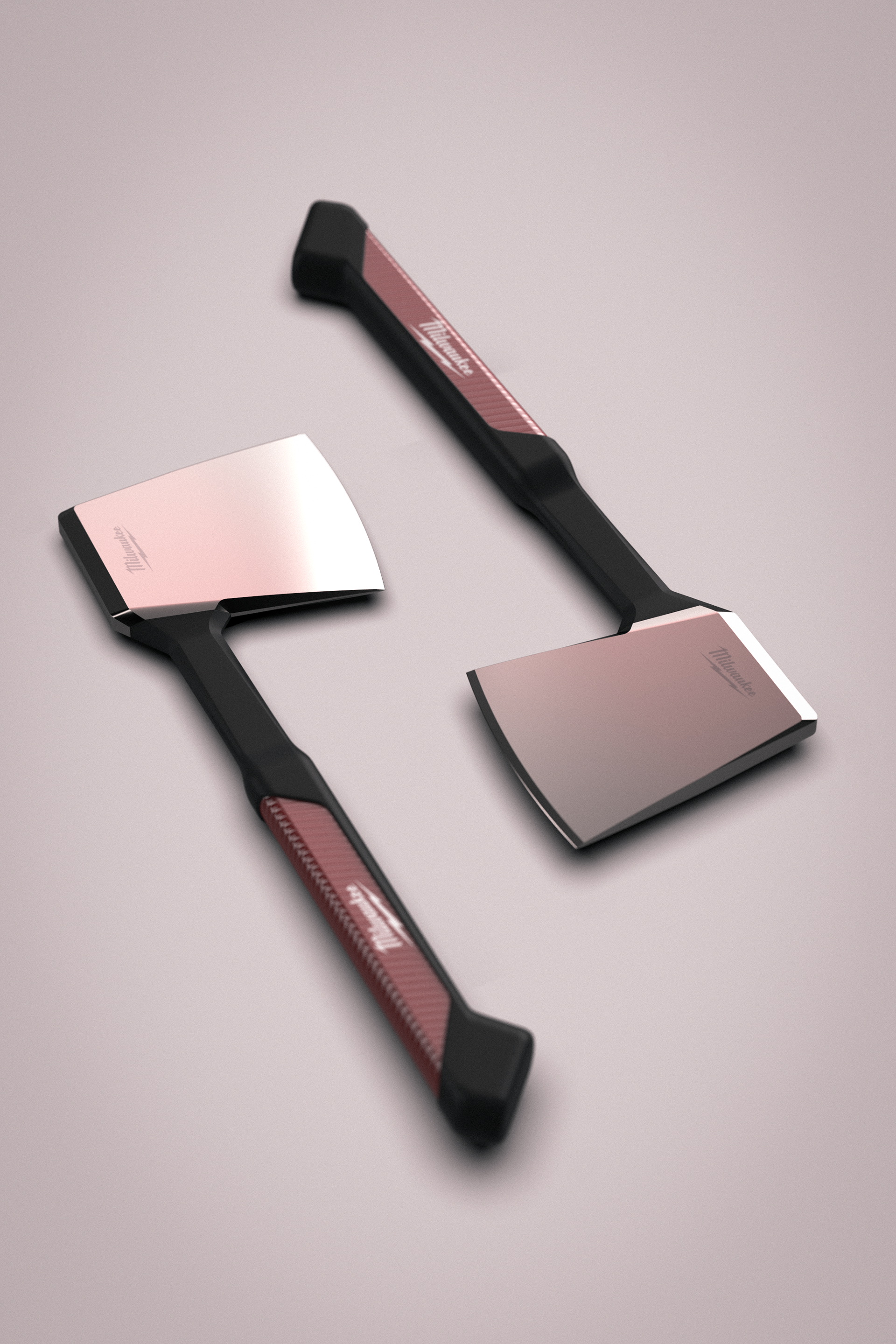
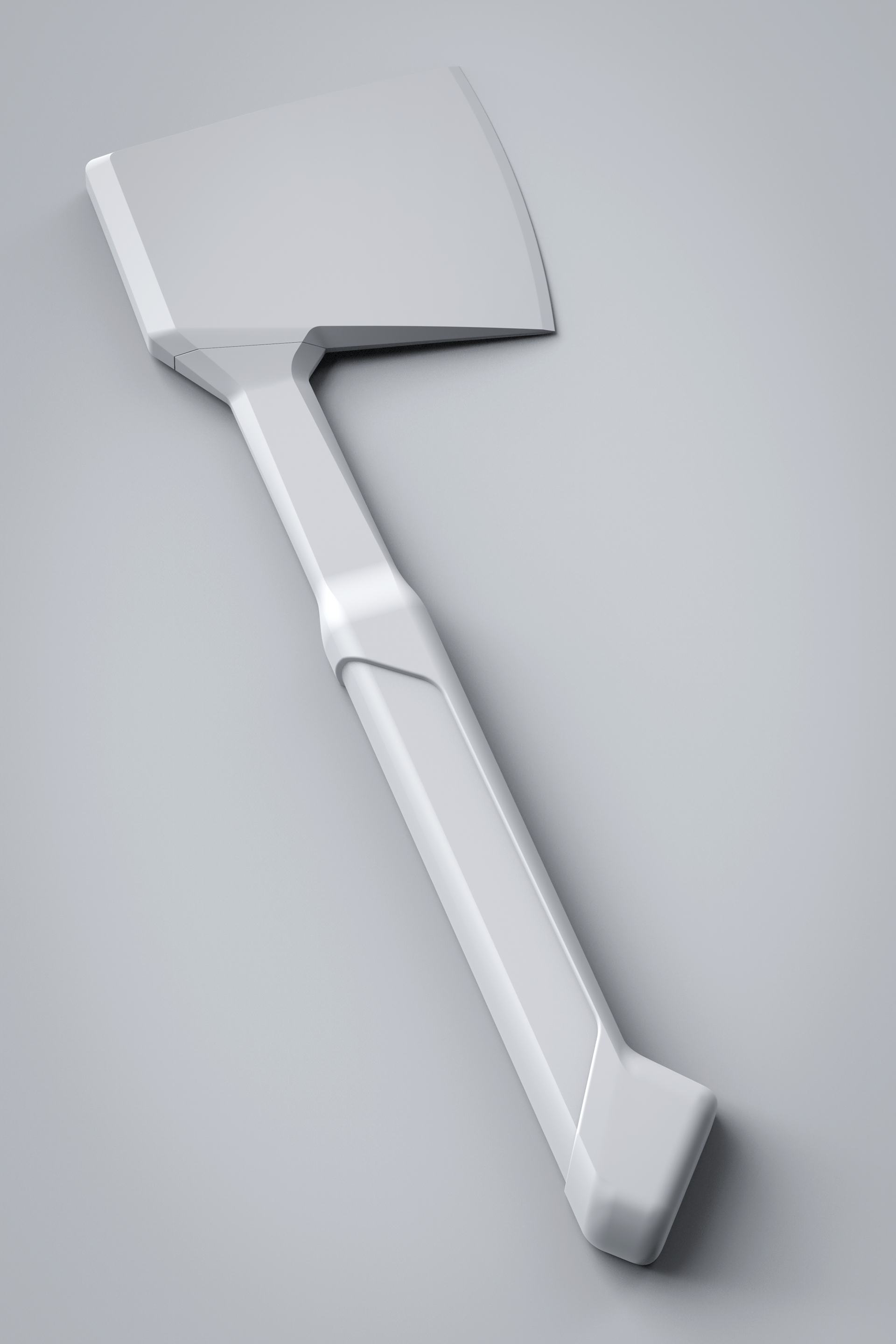
CAD rendering of the hatchet. Modeled in Solidworks, rendered in Keyshot.
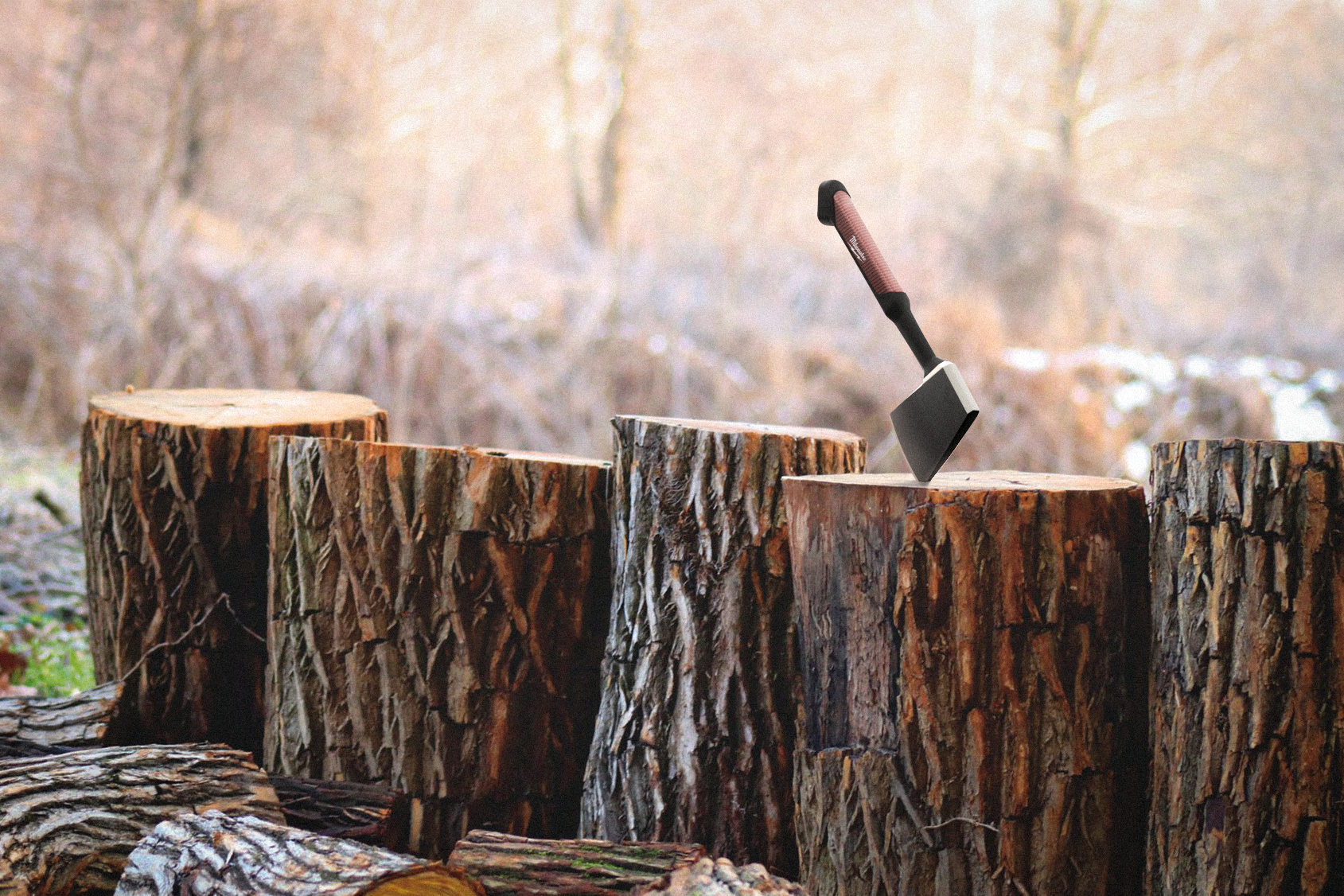